
L293D vs L298N Motor Driver: Key Differences Explained
Are you confused about whether to use the L293D or the L298N motor driver in your next project? While both are popular motor driver ICs, they serve different purposes based on voltage, current handling, and configuration needs.
In this blog, we’ll break down the difference between L293D and L298N motor drivers, discuss what an H-Bridge is, and help you decide which one is best suited for your robotics or automation project.
What is a Motor Driver and Why Do You Need One?
A motor driver acts as an interface between a microcontroller and a motor. It allows a low-power microcontroller, like an Arduino or an 8051-based chip, to control high-power DC motors that typically require more current and voltage than a microcontroller can provide.
If you connect a motor directly to a microcontroller, you risk burning out the pins or damaging the chip. Motor drivers like the L293D and L298N solve this by acting as current amplifiers that supply the motor with sufficient power.
Understanding the H-Bridge Circuit
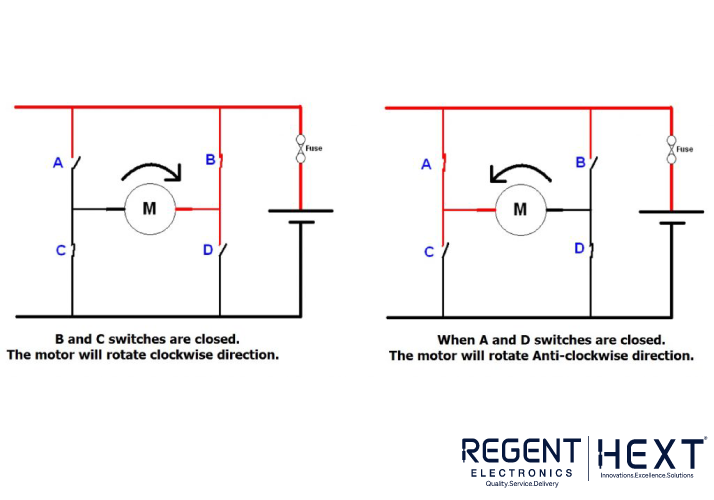
Before diving into comparisons, let’s talk about a core concept—H-Bridge.
An H-Bridge is an electronic circuit that allows voltage to be applied across a motor in both directions. This enables:
- Forward and reverse motion
- Braking
- Freewheeling (coasting)
H-Bridge circuits can be implemented using discrete components or integrated into motor driver ICs like the L293D and L298N. The name “H-Bridge” comes from the typical layout of the circuit, which resembles the letter “H.”
L293D vs L298N Motor Driver: A Side-by-Side Comparison

Here’s a detailed breakdown of how the L293D and L298N motor drivers differ:
Feature | L293D | L298N |
Operating Voltage | 4.5V to 36V | 7V to 46V |
Max Current per Channel | 600mA (up to 1A with heat sink) | 2A |
Driver Configuration | Quadruple Half-H Drivers | Dual Full-H Drivers |
Output Channels | 2 DC Motors or 1 Stepper | 2 DC Motors or 1 Stepper |
EMF Protection | Internal | External protection required |
Heat Dissipation | Minimal, often no heat sink | Includes heat sink for thermal safety |
Best Use Case | Low-current motors (e.g., BO motors, small DC gear motors) | High-current motors (e.g., Johnson motors, high torque gear motors) |
Form Factor | Compact, suitable for tight spaces | Larger, with heat sink mounting |
Key Differences Explained
✅ Voltage and Current Handling
- L293D is suitable for low-power applications, ideal for small robots or educational kits.
- L298N is better for high-power applications like robotic arms, RC cars, and automation systems.
✅ Configuration and Design
- L293D uses a half-H bridge design, offering four drivers.
- L298N uses a full-H bridge design, delivering higher current with fewer drivers.
✅ Heat Management
- L298N typically comes with an onboard heat sink to handle the high current load.
- L293D does not usually require one, making it more compact and easier to embed in lightweight builds.
✅ EMF Protection
- L293D comes with internal diodes to protect the circuit from back EMF.
- L298N needs external flyback diodes for safe operation, especially when dealing with inductive loads.
Bonus: L298N with Arduino UNO Combo
Regent Electronics also offers L298N motor drivers with an onboard Arduino UNO interface. This setup allows direct control of motors without the need for additional wiring, making it a plug-and-play solution for your DIY robotics or automation projects.
Price Comparison
Both the L293D and L298N motor drivers are available in the brushed DC motor driver category. The price difference is negligible—typically between INR 150 to 200, making them both budget-friendly options.
Conclusion: Which Motor Driver Should You Choose?
- Choose L293D if your motors are low-power (below 600mA) and you need a compact, beginner-friendly solution.
- Choose L298N if you’re driving high-torque motors or motors that require more than 1A of current per channel.
Understanding the technical requirements of your project is key to selecting the right motor driver. Whether you’re building a simple robot or a complex automation system, Regent Electronics has you covered with reliable, cost-effective motor driver solutions.
Frequently Asked Questions (FAQs)
Q: Can I use L298N for stepper motors?
Yes, L298N can drive bipolar stepper motors by controlling both coils independently.
Q: Is L293D enough for a line follower robot?
Yes, for basic line follower robots using BO motors, L293D is sufficient.
Q: What happens if I connect a high current motor to L293D?
It may overheat or fail. Always check the motor’s current rating before selection.
Still Confused? Let Us Help!
Drop a comment below or get in touch with Regent Electronics for personalized support on choosing the right motor driver.