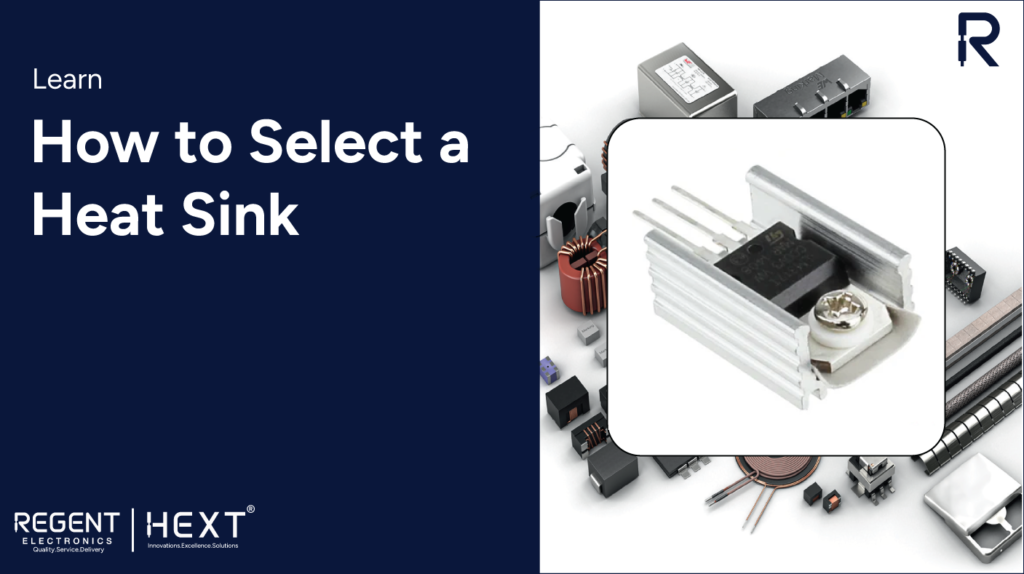
How to Select a Heat Sink for Optimal Thermal Management
Effective thermal management is crucial for the performance and longevity of electronic devices. Heat sinks are essential passive heat exchangers that help regulate temperatures by dissipating heat away from critical components. Whether you’re dealing with CPUs, power transistors, or LEDs, understanding how to select the right heat sink is vital for maintaining device performance. This guide will help you make informed decisions on heat sink selection for various applications.
What is a Heat Sink?
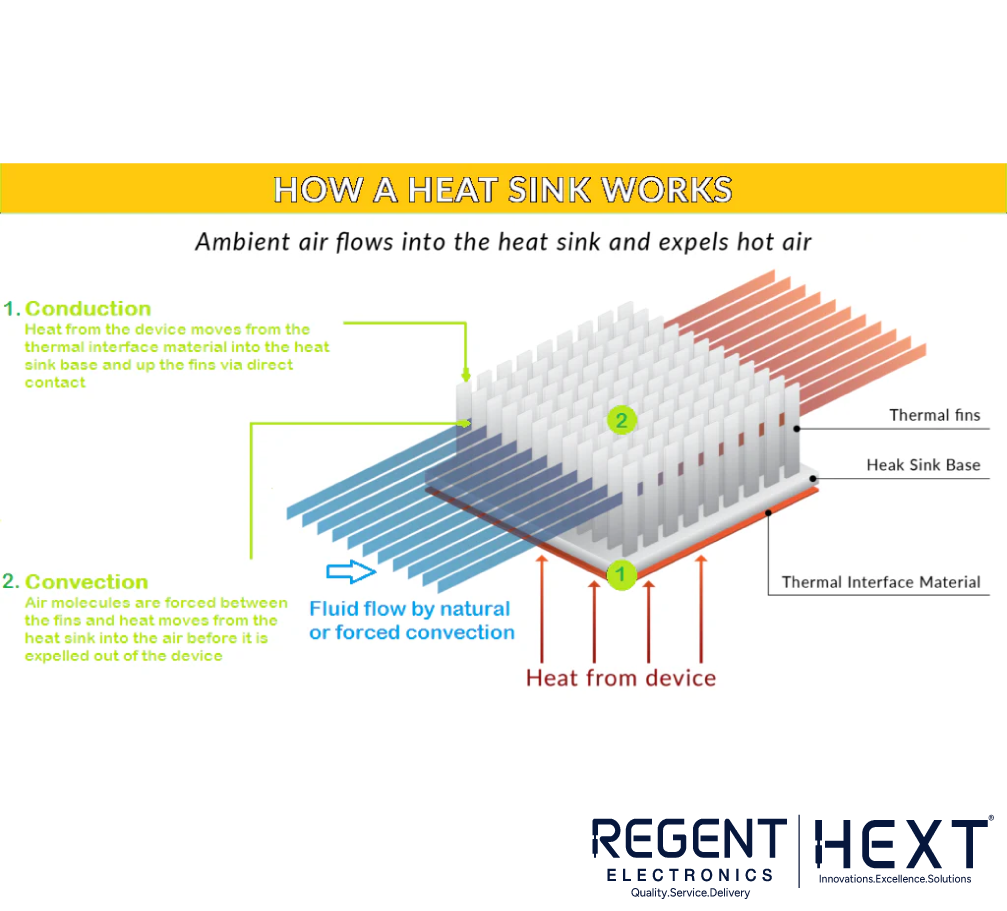
A heat sink is a passive component designed to transfer excess heat generated by electronic devices to a cooler medium, usually air or liquid. This heat dissipation process is essential for maintaining safe operating temperatures and preventing overheating. Heat sinks are commonly used in high-power devices like CPUs, GPUs, transistors, and LEDs, where natural heat dissipation may not suffice.
How Heat is Transferred
Heat can be transferred in three primary ways:
- Conduction: The direct transfer of heat through materials from a higher temperature area to a lower one.
- Convection: Heat transfer via fluid motion, usually air or liquid, where heat moves away from the device and is replaced by cooler fluid.
- Radiation: Heat transfer through electromagnetic waves, such as infrared radiation.
In electronics, conduction and convection are typically the most relevant methods for effective heat dissipation.
Step 1: Calculate Power Dissipation
The first step in selecting a heat sink is determining how much power the device dissipates. Power dissipation refers to the amount of heat the device produces during operation. To calculate power dissipation, use the formula:
Power Dissipation = (Vin – Vout) * Iout
For example, if a 7805 voltage regulator has an input of 9V and output of 5V with a current of 2A, the power dissipation would be:
Power Dissipation = (9V – 5V) * 2A = 8W
Step 2: Extract Thermal Resistance Values from Datasheets
After calculating power dissipation, refer to the component’s datasheet to extract the thermal resistance values. For instance, for a TO-220 package of a voltage regulator, the thermal resistance might be 19°C/W.
Step 3: Calculate Junction Temperature Without a Heat Sink
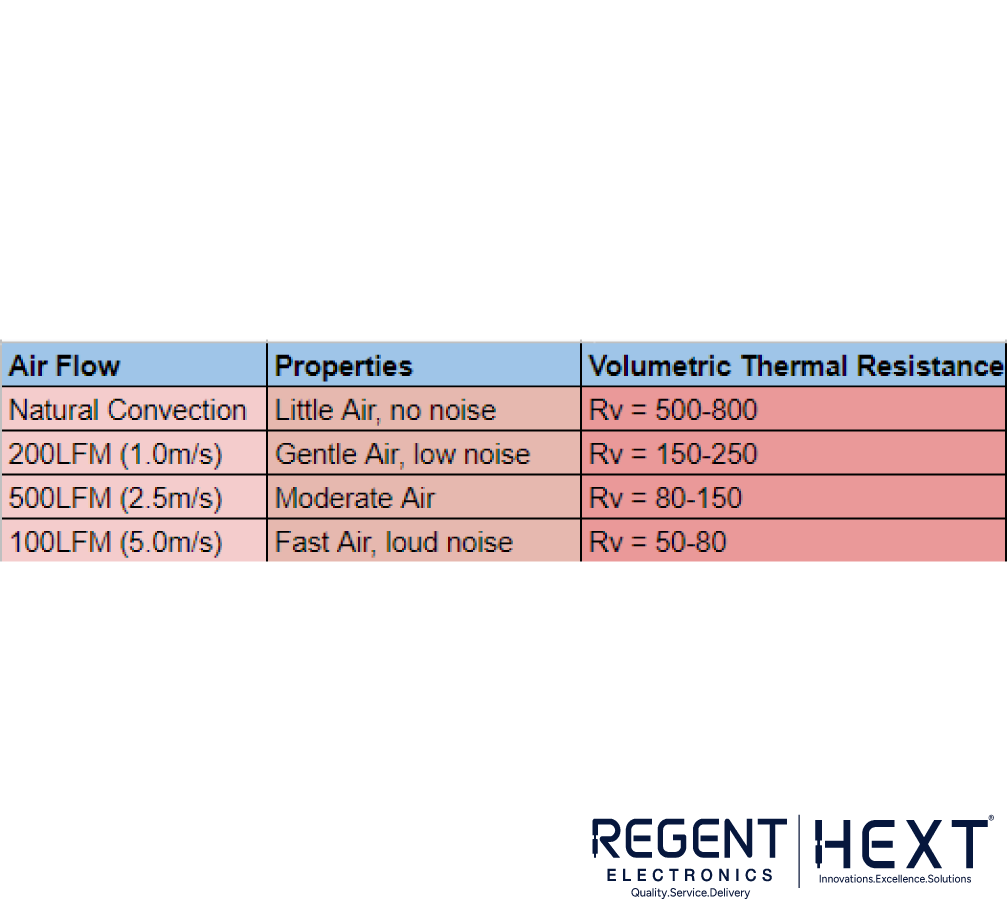
To assess the need for a heat sink, calculate the junction temperature using the formula:
Tj = Ta + R(JA) * Power Dissipation
Where:
- Tj is the junction temperature
- Ta is the ambient temperature
- R(JA) is the thermal resistance from junction to ambient
Assuming an ambient temperature of 35°C and a power dissipation of 8W:
Tj = 35°C + (19°C/W * 8W) = 187°C
Since the maximum operating temperature for most components is typically around 125°C, it’s clear that a heat sink is necessary.
Step 4: Calculate Junction-to-Case Thermal Resistance
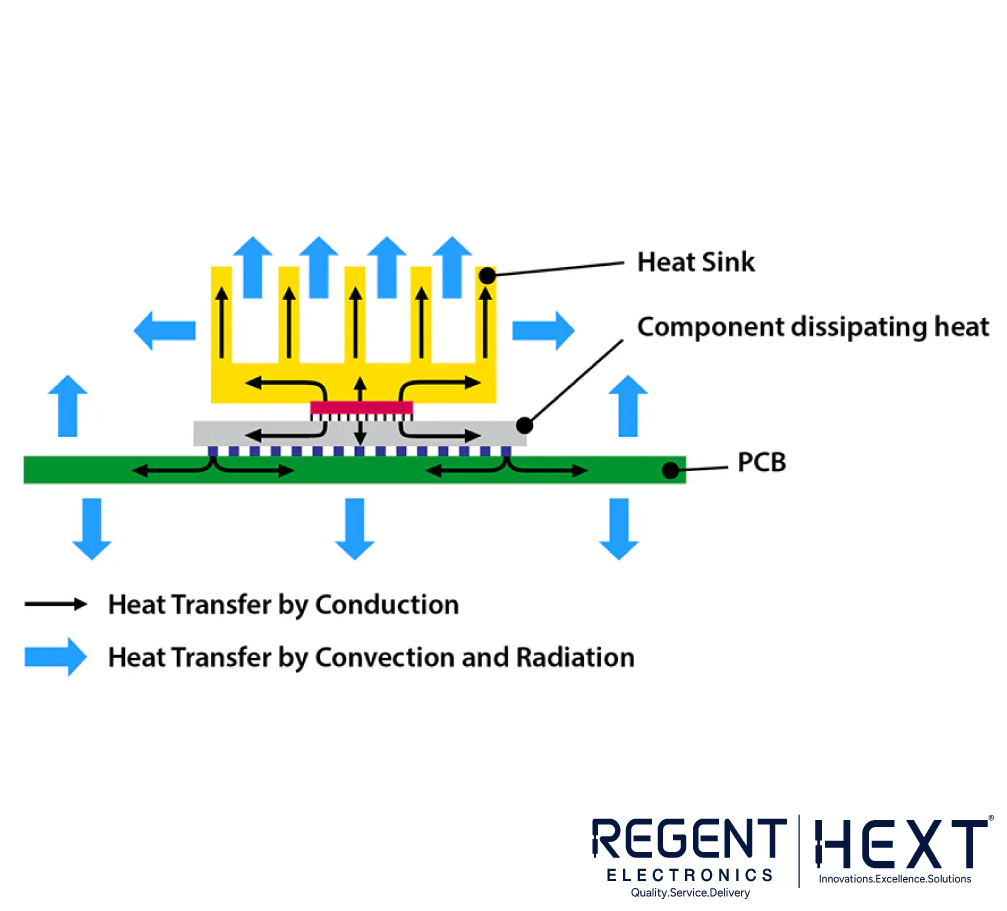
For more precise calculations, you’ll need the junction-to-case thermal resistance (R(JC)), which is available in the datasheet. For example, a component with R(JC) = 3°C/W helps estimate the junction temperature more accurately.
Step 5: Choose the Correct Heat Sink
Once you have the power dissipation and thermal resistance, the next step is selecting the right heat sink. Here’s how:
- Heat Source Power (Q): The thermal design power (TDP), or the amount of heat the device produces, should be provided by the manufacturer.
- Tc Max: The chip case’s maximum temperature, usually specified by the manufacturer.
- Max Ambient: The maximum ambient temperature where the device will operate.
- Thermal Budget: The difference between Tc Max and the Max Ambient, which dictates the total allowable temperature rise.
- Volumetric Thermal Resistance (Rv): This value helps estimate the heat sink’s required volume. The equation is:
V = (Q * Rv) / ΔT
Where ΔT is the temperature rise.
Select an Rv value based on the airflow across the heat sink. For example, with moderate airflow (2.5 m/s or 500 LFM), use an Rv between 80-150 for proper heat dissipation.
Step 6: De-Rating for Altitude
When operating at high altitudes, de-rate the Rv by 10% for each mile above sea level. For example, at 1 mile high, divide the Rv by 0.9 to adjust for the decreased air density.
Factors Influencing Heat Sink Performance
To maximize thermal efficiency, consider the following:
- Heat Sink Design: The shape, size, and arrangement of fins are critical. Fins should be arranged to optimize airflow.
- Airflow Direction: Ensure the airflow is parallel to the fins for maximum heat transfer.
- Air Speed: Faster airflow enhances heat dissipation.
- Material: Copper and aluminum are the most common materials for heat sinks, with copper offering better thermal conductivity.
- Thermal Interface Material: Use heat-conductive paste or thermal pads to improve heat transfer between the component and the heat sink.
- Thermal Resistance: Lower thermal resistance ensures better heat dissipation.
Types of Heat Sinks
There are two main types of heat sinks:
- Active Heat Sinks: These incorporate a fan or other active cooling methods.
- Passive Heat Sinks: These rely solely on natural convection and conduction.
Peltier Heat Sink (TEC1-12706) is an example of an active heat sink used in thermoelectric cooling systems.
Conclusion
Choosing the right heat sink involves understanding power dissipation, thermal resistance, airflow, and the device’s operational environment. By following these steps, you can ensure optimal thermal management, extending the life and performance of your electronic devices. For best results, always refer to the datasheet for precise specifications and consult with experts at Regent Electronics for tailored solutions to your cooling needs.