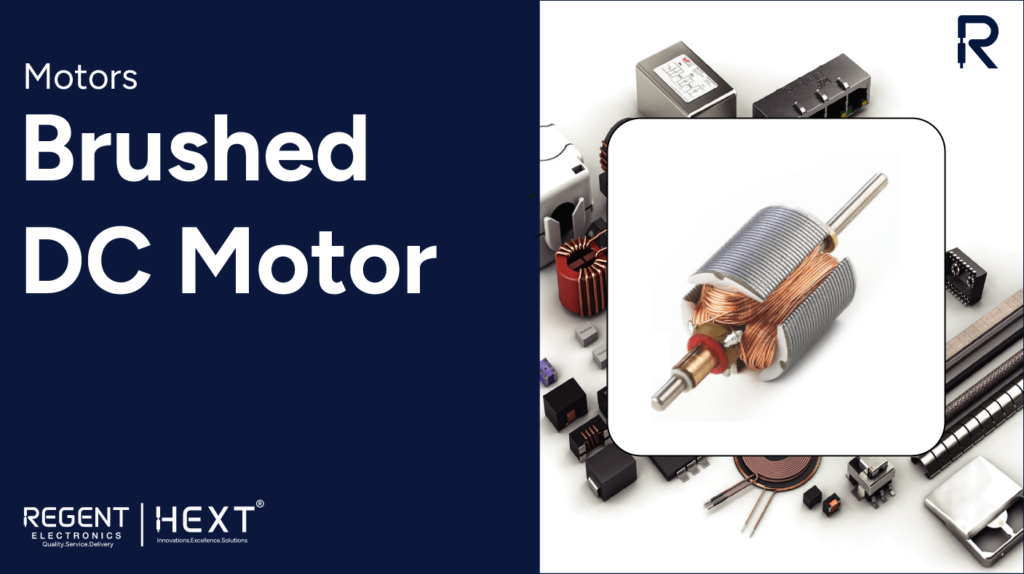
Brushed DC Motor: Working Principle, Construction, and Applications
Looking to understand how a Brushed DC Motor works? You’re in the right place. This guide by Regent Electronics explains the working principle, construction, advantages, disadvantages, and real-world applications of brushed DC motors in a clear and concise way.
🔧 What is a Brushed DC Motor?
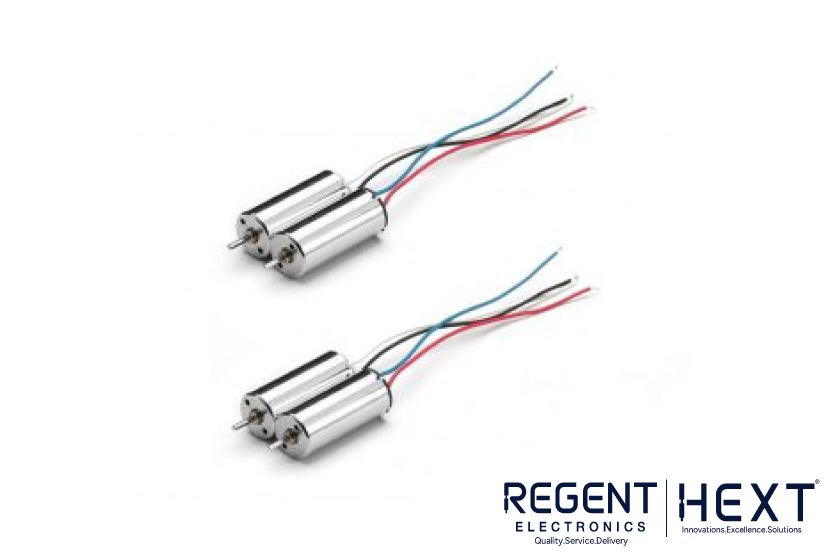
A Brushed DC motor is one of the earliest and most commonly used types of electric motors. Known for its simplicity, low cost, and ease of use, it is widely used in both consumer and industrial applications.
The term “brushed” refers to the use of carbon or metal brushes that transfer current to the rotating coil (armature) through a mechanical switch called the commutator.
⚙️ Construction of a Brushed DC Motor

The basic components of a brushed DC motor include:
- Stator: Houses two or more permanent magnets that create a magnetic field.
- Rotor (Armature): A coil wound on an iron core that rotates within the stator’s magnetic field.
- Commutator: A rotary switch connected to the rotor that reverses the current direction.
- Brushes: Stationary contacts that transfer current from the power supply to the rotating commutator.
💡 Key Point: The armature windings are located on the rotor, while the permanent magnets are placed on the stator.
⚡ How Does a Brushed DC Motor Work?
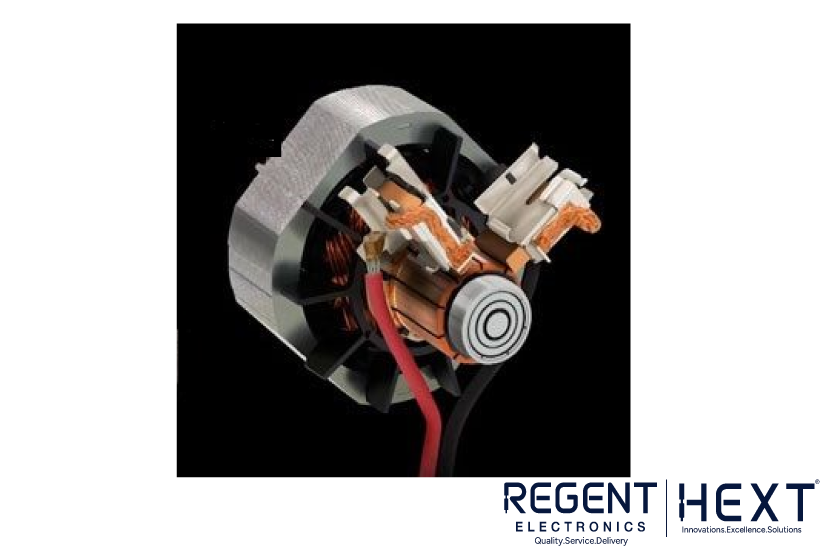
The working principle of a brushed DC motor is based on Faraday’s Law of Electromagnetic Induction and Lorentz Force. Here’s a step-by-step explanation:
- Power Supply: When DC power is applied, current flows from the source through the brushes and commutator to the rotor windings.
- Magnetic Interaction: The energized rotor winding creates a magnetic field, which interacts with the magnetic field of the permanent stator magnets.
- Rotation Begins: The interaction between these magnetic fields generates a force (Lorentz force) that causes the rotor to turn.
- Commutation: As the rotor spins, the commutator reverses the current direction, ensuring continuous rotation.
📌 Torque and speed are directly influenced by the applied voltage and the strength of the magnetic field.
✅ Advantages of Brushed DC Motors
- ✔️ Simple construction and low manufacturing cost
- ✔️ No need for a controller in fixed-speed applications
- ✔️ Easy to operate and maintain
- ✔️ Can often be repaired or rebuilt for extended use
- ✔️ Performs well in extreme environmental conditions
⚠️ Disadvantages of Brushed DC Motors
- ❌ Lower efficiency due to friction and electrical losses
- ❌ Generates electrical noise due to continuous contact and commutation
- ❌ Shorter lifespan because brushes and commutators wear out over time
- ❌ Requires periodic maintenance and replacement of brushes
🛠️ Common Applications of Brushed DC Motors
Despite the rise of brushless technology, brushed DC motors are still widely used due to their simplicity and affordability.
🔹 Household Applications:
- Electric toothbrushes
- Hairdryers
- Blenders
- Vacuum cleaners
🔹 Industrial Applications:
- Paper and textile machinery
- Cranes and hoists
- Conveyor systems
- Steel rolling mills
- Electric propulsion systems
🔹 Automotive and DIY:
- Power tools
- Model cars
- RC vehicles
- Small robotics projects
🧠 Final Thoughts
Brushed DC motors remain a reliable and cost-effective solution for a wide range of applications, particularly where simple control and low-speed torque are needed. Although they require more maintenance than brushless alternatives, their ease of operation and affordability keep them relevant in many industries.